Controllo di processo e controllo qualità sono due facce della stessa medaglia: la ricerca dell’ottimizzazione dell’una senza intervenire sull’altra in tempo reale è sempre inefficiente. Integrare sistemi di acquisizione e controllo dei dati in tempo reale con sistemi in grado di leggere la qualità del prodotto, come i sensori di spettroscopia NIR (Near InfraRed) di Buchi Italia (attiva da anni nel settore dei controlli di processo in linea tramite la Spettroscopia NIR), consente di analizzare la qualità del prodotto in ogni fase della produzione e di identificare le cause precise di ciascuna delle caratteristiche analizzate. La possibilità di intervento e ottimizzazione generata da questa integrazione offre un livello di controllo mai raggiunto prima che può fare la differenza sulla sostenibilità di un impianto.
Indice degli argomenti:
Il controllo qualità: le sfide del processo produttivo
Il controllo qualità è ormai, tanto nei mercati consumer che nel mondo dei semilavorati, un elemento fondamentale del processo produttivo. Se nelle produzioni B2C, il prodotto finale è sottoposto a richieste regolamentari e alle aspettative crescenti dei decisori d’acquisto, nel B2B la qualità della materia in ingresso nel ciclo produttivo può cambiare enormemente il prodotto finale.
Già pensando, per l’appunto, alla variabilità delle materie prime, ci rendiamo conto di quanto possa essere tardivo il classico controllo qualità sul prodotto in uscita. Immaginiamo, allora, quante altre variabili intervengono all’interno di un ciclo produttivo (che può durare anche molto a lungo), e il loro impatto sul prodotto finale.
Nonostante le analisi di laboratorio ex-post evitino l’immissione nel mercato di prodotti che non rispettano gli standard, di certo questo approccio non impedisce sprechi per l’azienda. Scoprire, infatti, solo a fine processo che c’è stata una deriva di produzione o che una fase chiave ha variato la composizione del prodotto, comporta non solo che quel lotto non possa essere venduto, ma anche che i costi dell’intero ciclo (energetici, di risorse umane, di usura macchina, di materie prime) sia di fatto sprecato.
La sfida di oggi nel mondo industriale sta non solo (o non tanto) nella digitalizzazione dei processi, ma soprattutto nell’utilizzo reale dei dati disponibili (segnali di macchina, dati di sensori e di laboratorio), che per quanto precisi generano una mole di dati di difficile gestione e spesso, anche, di difficile lettura.
Il machine learning nell’ottimizzazione di processo
Strumenti avanzati di intelligenza artificiale, pensati a adattati alle esigenze specifiche di ogni processo produttivo come i modelli di machine learning e di analisi predittiva, sono il mezzo migliore, ad oggi, per consentire all’azienda non solo di integrare e rendere leggibili i dati, ma anche di trasformare i classici strumenti di SPC (Statistical Process Control) in informazioni e indicazioni chiare di ottimizzazione del processo. Non solo: questi modelli consentono di correlare dati diversi in modelli predittivi, per intervenire preventivamente ed evitare o interrompere eventuali derive e malfunzionamenti del processo prima che impattino su un’intera produzione.

I vantaggi della spettroscopia nel vicino infrarosso
La spettrometria NIR (o del “vicino infrarosso”, in cui rientrano le lunghezze d’onda più corte nello spettro della luce IR) è da anni una valida alternativa alle metodiche analitiche classiche. La sua diffusione è iniziata nell’industria agro-alimentare dove è utilizzata per controlli non distruttivi per parametri quali umidità, proteine, grassi ecc.
Successivamente è stata impiegata anche nell’industria chimico-farmaceutica per il controllo delle materie prime, degli intermedi di lavorazione e per il prodotto finito.
Le analisi NIR sfruttano la radiazione nel vicino infrarosso, trasformando un segnale elettrico in un risultato analitico. Il campione è colpito da una radiazione assolutamente innocua che fa vibrare le molecole del campione, che reagiscono in modo diverso a seconda della concentrazione dei vari analiti. I segnali ottenuti sono elaborati matematicamente, restituendo alla fine le concentrazioni dei vari analiti richiesti. Non è quindi necessario l’utilizzo di consumabili o reagenti tossici che andrebbero poi smaltiti con costi latenti che a volte possono diventare elevati. Ne consegue che la spettrometria NIR risulta essere anche amica dell’ambiente, poiché non produce rifiuti. È inoltre considerata come un valido dispositivo per la sicurezza sugli ambienti di lavoro visto che a differenze delle analisi con le metodiche classiche di laboratorio, elimina l’uso di reagenti tossici e aggressivi che potrebbero creare infortuni al personale.
Altro aspetto interessante della tecnica NIR è l’assenza di preparazione del campione. Il prodotto da analizzare viene scansionato tal quale ed essendo un’analisi non distruttiva il campione può essere tenuto come contro campione o per le letture in linea, confezionato senza sprechi e senza costi aggiuntivi.
Tuttavia, la caratteristica principe di questa tecnica è la velocità. Si possono avere risultati analitici in pochi secondi sia in laboratorio che in processo.
In laboratorio per il controllo qualità risulta molto efficace perché dà la possibilità di controllare velocemente le materie prime addirittura prima dello scarico merci, evitando uno stoccaggio in azienda di prodotti non conformi. Ma i maggiori benefici si hanno con l’utilizzo in linea che permette di avere risultati in tempo reale, dando informazioni istantanee senza interrompere il processo produttivo. Questo integra la spettrometria NIR perfettamente con l’utilizzo dell’intelligenza artificiale che elaborando il dato acquisito insieme alle altre informazioni del processo, reagisce istantaneamente ottimizzando il processo.
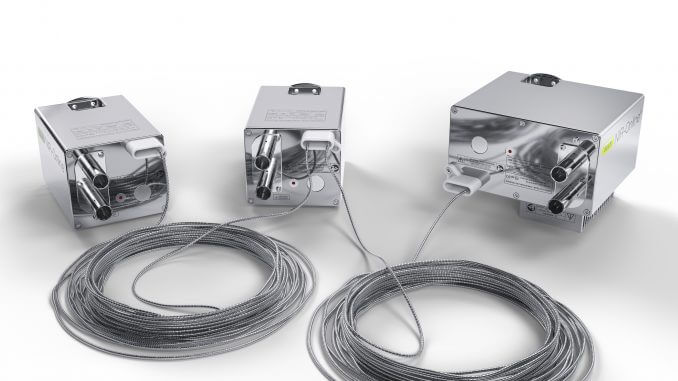
Monitoraggio in tempo reale del processo produttivo
Nel caso dei poliuretani, per fare un esempio, l’efficienza della sintesi del processo e la loro qualità dipendono fortemente sia dalla materia prima, che dai prodotti intermedi e dalla loro composizione.
La spettroscopia NIR può quindi essere impiegata sia al ricevimento merci, nelle fasi di lavorazione e per il controllo dei prodotti finiti.






Per ogni caso e tipologia di prodotto, i momenti ideali di monitoraggio, i parametri analizzati e i punti di misura cambiano, ma l’adattabilità di questo strumento, rende questo approccio molto efficace nell’eliminazione dei fuori specifica nell’ambito dei processi produttivi.
La possibilità di integrare gli output di questo genere di sensori in strumenti avanzati di Statistical Process Control diventa la chiave per trasformare i dati di monitoraggio in previsioni. Questo consente di anticipare le derive e, così, prevenire la produzione dei fuori specifica.
Nuovi approcci alla gestione e ottimizzazione del processo produttivo
Se il controllo qualità è ormai strutturato anche dal punto di vista normativo in molti ambiti, il controllo di processo non è ancora oggetto ufficialmente di obblighi aziendali. Ciononostante (e soprattutto in considerazione del sempre maggior focus sulla sostenibilità nei bilanci ESG) l’ottimizzazione di processo sta acquisendo sempre maggiore rilievo nelle politiche aziendali.
Con la grande componente tecnologica di cui sono composti i processi manifatturieri, la chiave per poter attuare politiche di ottimizzazione è la corretta lettura e analisi dei dati prodotti dal processo stesso.
Il primo step che deve quindi svolgere una piattaforma ai based di data science dedicata al controllo di processo (come quella sviluppata da Kode) è quindi quello di raccogliere dati provenienti da diverse sorgenti. Questo tipo di soluzione include, nel caso ve ne fosse bisogno, un supporto alla digitalizzazione dei processi, consentendo di sostituire supporti cartacei con database e moduli di inserimento dati.
Per prendere decisioni solide e giustificate, però, è importante non solo poter visualizzare i dati di processo, ma anche valutare statistiche e indicatori che sintetizzino l’informazione disponibile e la rendano facilmente comprensibile. Tutte queste informazioni vengono integrate nel modulo SPC, in cui tutto il percorso di analisi è tracciato e ripercorribile, e consente di valutare eventuali criticità, di volta in volta diverse.
L’inserimento di modelli di correlazione tra le variabili di processo e le variabili di qualità del prodotto costituisce il reale plus del sistema. Infatti, in questo modo è possibile capire senza difficoltà come operare per ottimizzare il processo (sia in termini di resa che di qualità del prodotto), ma anche capire, facendo una root cause analysis, cosa non ha funzionato, in modo da calibrare meglio la produzione futura.
Sono molte le casistiche in cui questo genere di sistema dà risultati decisamente interessanti. Ad esempio, consente di capire:
- come pressione e velocità degli spruzzi di vernice impattano su resa e consumi nella produzione di prodotti in pelle
- come la programmata termica dei forni determina la resa e la qualità di piastrelle o di alimenti
- come l’afflusso delle materie prime e i tempi di residenza nei mixer influenza la resa di reazioni chimiche
- come il contenuto di umidità e proteine può far variare il valore di mangimi
- come la velocità di alimentazione di calandre e ribobinatrici comporta rotture del foglio di carta
Tutti questi esempi sembrano semplicemente guardare a un paio di aspetti di una produzione, ma sono decine (se non centinaia) le variabili di processo e i parametri di impianto che vanno a influenzare tanto la qualità del prodotto quanto gli altri aspetti del processo da tenere sotto controllo (consumo energetico, scarti, rilavorazioni…). È in questi casi reali che un sistema basato su AI si rivela estremamente utile, dal momento che è in grado di accogliere modelli di machine learning capaci di operare con centinaia e centinaia di variabili al tempo stesso.
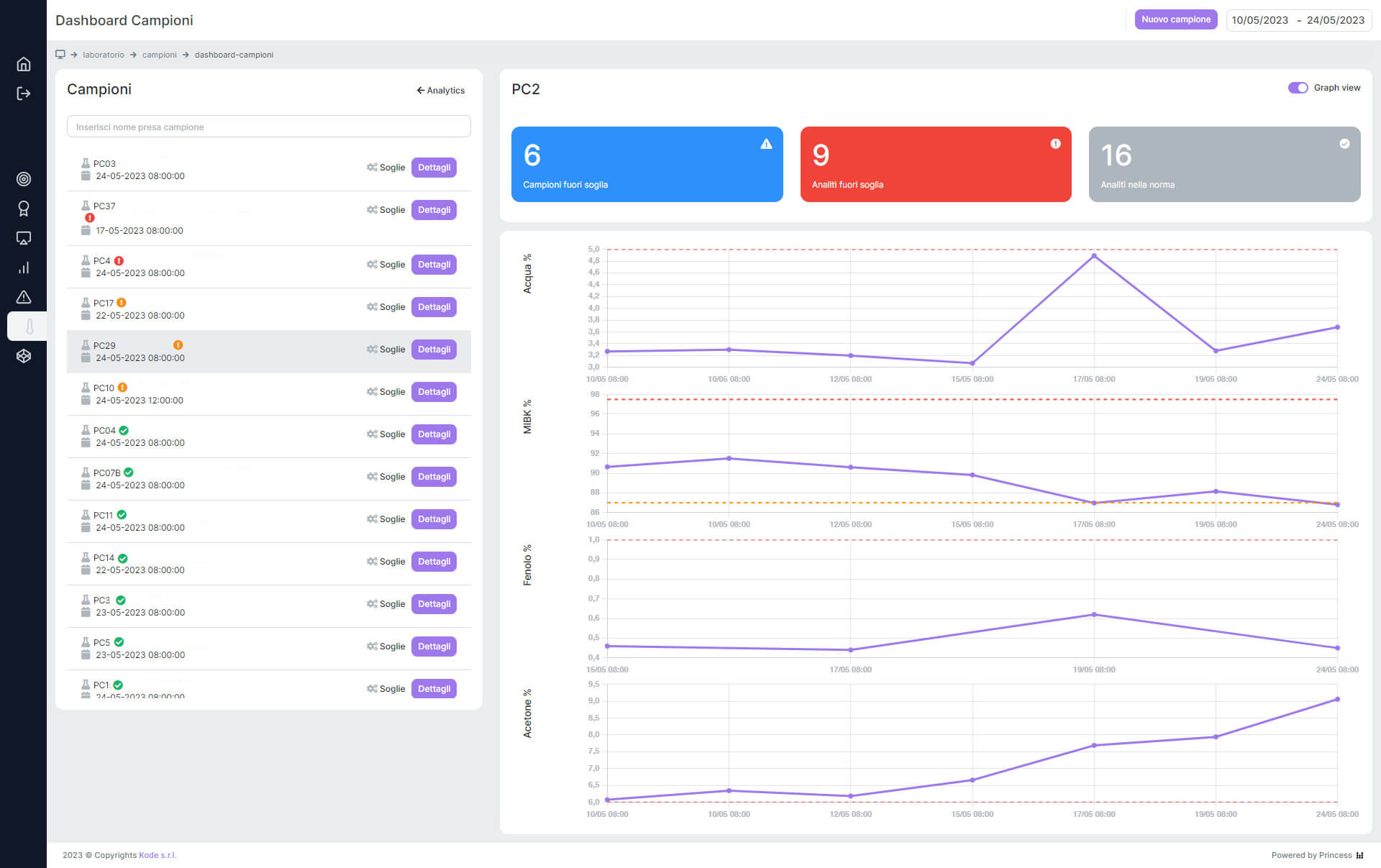
Come il controllo qualità si integra all’interno dei sistemi di gestione del processo produttivo
Un aspetto positivo molto importante garantito dal sistema creato da Buchi Italia è la possibilità di analizzare la qualità del prodotto in continuo, con un analizzatore on-line. Ciò significa che è possibile avere le informazioni necessarie senza dover portare i campioni in laboratorio, cosa che comporta un aumento dei tempi, dei costi e che comunque non fornisce una visione continua del processo, ma solo su alcuni momenti.
La visualizzazione dell’andamento delle caratteristiche del prodotto porta già un vantaggio evidente: quello di poter verificare in tempo reale quali prodotti siano fuori specifica.
Ma avere un’informazione precisa, continua e puntuale della qualità del prodotto, senza sapere con esattezza come mai siano stati ottenuti certi valori di qualità, rappresenta comunque una soluzione parziale.
Infatti, spesso, i prodotti che non rispondono agli standard qualitativi non sono dovuti a singoli e casuali eventi all’interno di un ciclo produttivo, ma sono generati da derive di processo o errori strutturali, che eventualmente si ripetono.
D’altro canto, avere un controllo di processo, per quanto avanzato, che non sia strettamente legato alla qualità del prodotto finito rappresenta una soluzione parziale, che consente solamente di capire se il processo è in controllo o meno, ma non necessariamente di valutare quantitativamente quanto lo stato di fuori controllo effettivamente impatti sulla qualità finale del prodotto.
È quindi immediato capire che l’unione dei dati di processo e delle materie prime coinvolte, con i dati di qualità del prodotto finito è un’importante chiave per il successo di un processo produttivo.
Da qui nasce l’idea di integrare expertise, skills, software e hardware di Kode e Buchi Italia in un’unica soluzione, in cui i parametri di qualità del prodotto vengono correlati ai parametri di processo e delle materie prime, e viceversa. Attraverso modelli di machine learning, che possono svolgere analisi multivariate su tutti questi dati, si è capaci di costruire proiezioni di scenari (anche mai analizzati prima), e così evitare errori e derive di produzione.
In questo modo se i parametri di processo o delle materie prime non rispetteranno standard o specifiche sarà possibile capire subito se e quanto questo possa impattare sulla qualità finale del prodotto, ancor prima di averlo prodotto!
Perché queste informazioni generino realmente ottimizzazione e riduzione degli sprechi, è necessario che esse si traducano in tempestivi interventi sul processo. A questo scopo sulla base di modelli predittivi robusti e stabili, possono anche essere implementati automatismi nel processo stesso, che, a seguito della previsione di non conformità del prodotto finito, riportino il prodotto in specifica, evitando che si formino scarti.
Ove non si volesse arrivare a questo livello di automatizzazione, nel caso di prodotto non conforme, l’integrazione dei due tipi di dati tracciati in tempo reale in uno strumento di SPC avanzato, consente di capire immediatamente quali possano essere le cause, anche se le variabili di processo fossero centinaia, affinché gli operatori di impianto possano intervenire adeguatamente.
Si tratta di un livello di semplificazione dell’intervento sull’attività produttiva che non era di fatto neppure raggiungibile fino ad ora e che può veramente trasformare l’operatività di un’azienda.
Ambiti di applicazione e uso
Integrare questo genere di soluzioni non solo è utile, ma necessario per restare competitivi tanto nel mercato manifatturiero come nei settori ad alta industrializzazione.
Fortunatamente questo tipo di progetto, se condotto con partner che hanno esperienza, tanto di dominio (intelligenza artificiale, Data science) quanto del settore produttivo dell’azienda, non richiede più tempi e investimenti titanici, ma solo un adeguato design.
Questo tipo di soluzione integrata, infatti può essere applicata a molti ambiti produttivi: da qualsiasi genere di prodotto chimico e farmaceutico alla produzione alimentare (mangimi, prodotti lattiero – caseari, granaglie e sfarinati), ma anche la produzione di semi oleosi, olii vegetali e biodiesel, la produzione di zucchero o di bioetanolo… La gamma di settori industriali che possono sfruttare questo tipo di soluzioni è molto vasta.
L’integrazione si differenzia da caso a caso per piccoli aspetti: i punti e i macchinari in cui integrare i sensori di Buchi, il tipo di connettore, il processo di normalizzazione dei dati, o gli indicatori e algoritmi da costruire; tutti aspetti su cui adattiamo normalmente questi strumenti. Questo significa che, finalmente, l’ottimizzazione di processo è ormai accessibile anche alle aziende di media dimensione e con vantaggi importanti.